Electrical PVC pipes are essential components in modern electrical installations. These pipes are designed to provide safe, reliable, and durable protection for electrical cables and wiring systems. They are used in a wide range of applications, from residential and commercial buildings to industrial and outdoor environments, ensuring that electrical wiring is safely housed and protected from external factors such as moisture, chemicals, and physical damage.
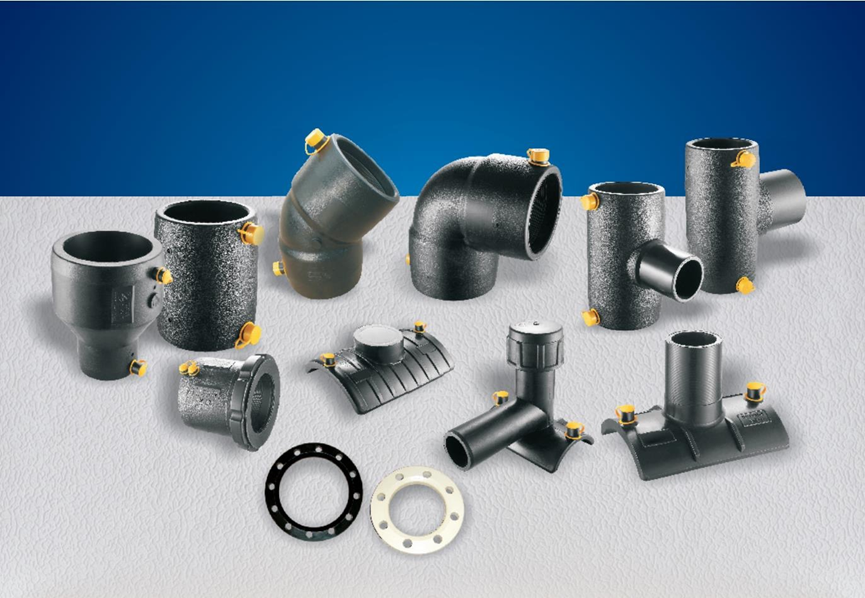
1. Material Preparation
The first step in the manufacturing process of electrical PVC pipes is material selection and preparation. High-quality PVC resin is the primary material used to manufacture electrical pipes. PVC resin is mixed with additives to enhance the pipe’s properties, such as impact resistance, flame resistance, chemical resistance, and UV protection. The blend may also include stabilizers, lubricants, and plasticizers to improve the pipe’s workability and ensure it meets the necessary performance requirements.
Once the PVC mixture is prepared, it is sent for extrusion, where it is heated and formed into a pipe shape.
2. Extrusion
The extrusion process is a critical step in the production of electrical PVC pipes. In this step, the prepared PVC compound is fed into an extruder machine, which uses heat and pressure to melt the material and push it through a mold. The PVC is shaped into the desired pipe diameter and thickness during this process.
The extruder machine works by forcing the melted PVC through a die, which gives the pipe its final shape. The extruder also maintains consistent pressure and temperature, ensuring the pipe is uniform in size and smooth on the inside and outside. This is essential to prevent electrical wires from being damaged during installation or use.
3. Cooling and Solidification
After extrusion, the soft, hot PVC pipe is cooled and solidified. The pipe is passed through a cooling tank or a series of water baths to lower the temperature and harden the material. Cooling is essential because it ensures the pipe retains its shape and becomes firm enough for the next stages of production.
This cooling process also allows the pipe to gain the strength and rigidity required for electrical conduit systems. The PVC pipe is now strong enough to withstand external stresses such as impacts or compression during installation.
4. Cutting to Length
Once the pipe has cooled and solidified, it is cut into specific lengths according to customer specifications or industry standards. The cutting process is typically automated, with a cutting machine or saw ensuring precision and accuracy. The cut pipes are then ready for further processing or packaging.
Some manufacturers may also choose to offer custom lengths of electrical PVC pipes, depending on the needs of their clients.
5. Surface Treatment and Inspection
The next step is surface treatment and inspection. In this stage, the pipes undergo visual and mechanical inspections to ensure they meet the required standards for strength, smoothness, and uniformity. Any defects, such as cracks, discoloration, or surface imperfections, are identified and removed.
Marking is also applied during this stage. This typically includes printing the manufacturer’s logo, size, and other relevant information, such as the maximum pressure rating and certification marks. For electrical PVC pipes, it’s important to ensure that the markings comply with regulatory requirements.
6. Quality Control and Testing
Quality control is one of the most important stages of the manufacturing process. During this stage, the electrical PVC pipes are subject to various tests to ensure they meet industry standards, including:
– Impact resistance testing: This ensures that the pipes can withstand physical forces during installation or operation without cracking or breaking.
– Pressure testing: Electrical PVC pipes must be able to handle internal pressure without deforming. Testing ensures that the pipes meet pressure resistance requirements.
– Flame resistance testing: Electrical PVC pipes must comply with fire safety standards. The pipes are tested for their ability to resist combustion and prevent the spread of fire.
– Chemical resistance: Electrical PVC pipes should resist chemical reactions with substances like oils, fuels, or solvents. Testing ensures that pipes will not degrade when exposed to chemicals.
These tests guarantee that the pipes are safe, reliable, and capable of performing under the conditions they will face once installed.
7. Packaging and Distribution
After passing quality control, the pipes are packaged for distribution. Packaging materials are chosen to protect the pipes during transit and storage, ensuring that they reach their destination without damage. The pipes are bundled, labeled, and packed into boxes, and are then ready for shipment to customers or retailers.
Conclusion
When it comes to high-quality electrical PVC pipes, LESSO is a trusted name in the industry. LESSO’s commitment to advanced manufacturing techniques, rigorous testing, and superior quality materials makes them a reliable choice for electrical installations. Whether you’re looking for electrical conduit for residential, commercial, or industrial use, LESSO’s electrical PVC pipes meet the highest standards for durability, safety, and performance.